- Vacuum Annealing Furnace 1800¡ãC
- Vacuum Sintering Furnace
- Heat Treatment Furnace
- Drop Bottom Sintering Furnace
- Car Bottom Furnace
- Roller Hearth Furnace
- Mesh Belt Furnace
- Continuous Mesh Belt Furnace
- Ceramic Tiles Roller Furnace
- Roller Kiln
- Industrial Kilns
- Shuttle Kiln
- Tunnel Kilns
- Bogie Hearth Furnaces
- Rotary Kilns
- Pusher Kilns
- Ceramic Roller Kilns
- Sintering Furnace
- Annealing Furnace
- Vacuum Heat Treatment Furnace
- Vacuum Hardening Furnace
- Tempering Furnace
- Continuous Heating Furnace
- Crucible Furnace
- Glass Melting Furnace
- Muffle Furnace
- Gold Melting Furnace
West Of Kelong South Road, Luoxin Industrial Park, Xinan County, Luoyang, Henan, China.
+86-379-60193738
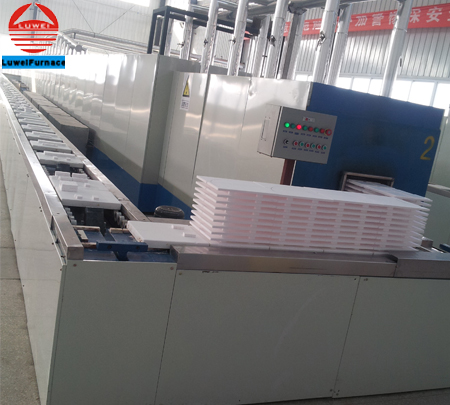
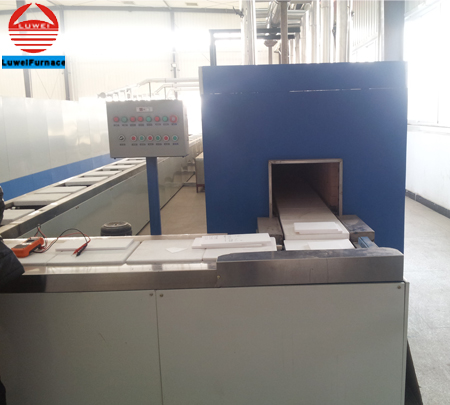
Pusher Kilns
- Brand Name: Luwei
- Model: Ceramics continuous production line Pusher Kilns
- Max.Temperature: 1200°C
- Working Temperature: 1200°C
- Furnace Chamber Size: 150*300*13000MM
- Temperature Controller: PID and SCR
- Control Accuray: ± 1°C
- Heating Element: SiC rods
- Thermocouple: S type
- Chamber Material: High purity Ceramic fiber
Pusher Kilns and tunnel kilns are ideal for processes requiring precise control of temperature and atmosphere, for those with longer residence times that require exact control of the heat up rate of the product (temperature profile), and those with a lower gas/solid reaction.
The Pusher Kiln has a hydraulic system that pushes load trays (ceramic or metal) through the kiln tunnel. The trays may push through various zones of temperature to meet a particular temperature profile. For larger load sizes, more than one tray may be pushed in at a time. When the trays reach the exit end of the kiln, they may be manually or automatically returned to the entrance end for reloading. As in the Car Kiln, the entire process can be automated to be safer and more efficient.
Pusher Kilns is mainly used in the production of ceramic tiles table dishware bone teaset pottery bowls ceramic gifts and other ceramic building materials. Pusher Kiln is continuous heating and work it is made by the rotation of the ceramic tube as the roller kiln vehicle the ceramic tiles or bricks materials in the kiln inner chamber.
Technical Specifications of Pusher Kilns |
|
Chamber size |
150x350x13000mm (Height * Width* Depth) |
Max. temperature |
1200°C (<2hour) |
Working temperature |
1200°C |
Temperature controlling |
PID automatic control via SCR (Silicon Controlled Rectifier) power control with phase angle fired, current limiting resistor. |
16 programmable segments for precise control of heating rate, cooling rate and dwell time. |
|
Built in PID Auto-Tune function with overheating & broken thermocouple broken protection. |
|
Over temperature protection and alarm allows for operation without attendant. |
|
Temperature accuracy |
±1°C |
Heating rate |
0-15°C/min |
Thermocouple |
Long life S type with 99.7% purity Alumina tube |
Heating elements |
SiC Heating element |
Furnace Chamber |
Three layers of ceramic fiber insulation materials |
Furnace structure |
Double layer steel casing with dual cooling fan, surface temperature below 60°C |
Furnace door |
Front-side open |
Power cutting off when furnace door open |
|
Working voltage |
220V or 380V, 50HZ or 60HZ |
Rated power |
180 KW |
N.W/G.W |
3600KG/4200KG |
Stander chamber size (mm)customize |
200x100x3000 250x100x3000 300x150x3000 350x80x5000 350x80x8000 250x50x10000 |